Before
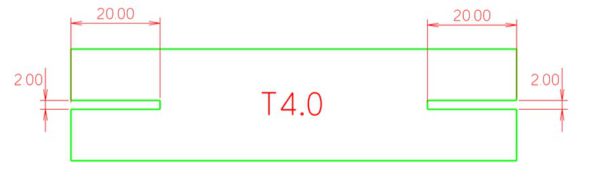
切削加工品のコストダウンを行うために押さえておくべきポイントは様々ありますが、今回はそれらの中でも、設計者の方に比較的容易に取り入れて頂きやすい事例をお伝え致します。
Beforeの図をご覧ください。厚み4mmのプレートに幅2mmの溝(長穴)が設計されています。この形状を縦型マシニングセンタのみで実現しようとした場合、溝の底部が直角になっていることから、まずプレートを立てて固定してからエンドミルで加工する必要があります。しかし、通常φ2のエンドミルは6mmまでしかなく、20mmもの溝を加工することはできません。
コストダウン事例
After
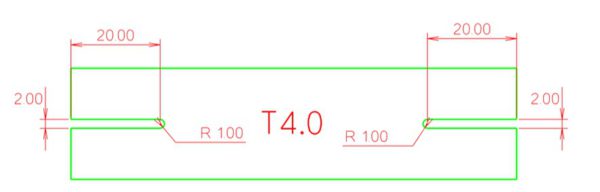
溝形状の部品を設計する際には、それを実現するためにどんな工具を用いるか、想像しながら行うと容易にコストダウンを行うことができます。
Beforeのように溝の底部を直角にするとエンドミルの先端部を使って加工しなければ実現できませんが、Afterのように溝底部の形状を1Rにすると、プレートの側面からの工具をアプローチすれば加工が可能となります。従って、市販されているφ2のエンドミル一発で加工することができるので、コストダウンとなります。
機械部品を設計する際には、なるべくドリルやエンドミルなどの標準の切削工具のみで実現できる形状にするとコストダウンになります。今回の事例も、例えばワイヤーカット放電加工機を用いれば加工できますが、加工時間が掛かってしまってコストが上昇してしまう可能性があります。
ただ設計者の皆様は、機械の設計をしながら膨大な量の図面を作成する必要があり、一つひとつの部品に対して使用する工具を想定して図面に反映するというのはとても難しいことと思います。そこで機械加工+溶接.comを運営する三栄製作所では、今回の事例のように頂いた図面に対するコストダウンに繋がるVE提案を積極的に行うサービスを行っております。もしお悩みの案件がございましたら、お気軽にご相談ください。
ただ設計者の皆様は、機械の設計をしながら膨大な量の図面を作成する必要があり、一つひとつの部品に対して使用する工具を想定して図面に反映するというのはとても難しいことと思います。そこで機械加工+溶接.comを運営する三栄製作所では、今回の事例のように頂いた図面に対するコストダウンに繋がるVE提案を積極的に行うサービスを行っております。もしお悩みの案件がございましたら、お気軽にご相談ください。