Before
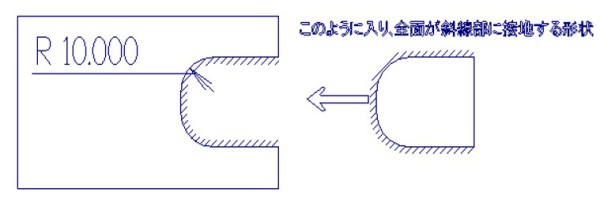
今回ご紹介するコストダウン事例は、「旋盤加工品は使い方を反映した形状でコストダウン!」です。
たとえばこのBefore図のように、先端がR10の形状を持つ市販品や購入品の軸を使用し相手物に挿入しなければならない場合、当然相手物には内径加工が必要になりますが、こうしたケースでは多くの場合、「相手物に合わせて設計してしまう」ことが多くあります。つまり今回の事例で言うと、R10を持つ凹形状にしてしまう、といったことです。
設計する方の意向としては、挿入する部品のすべての面を設置させて安定させたい、という意思が働いての事だと思いますが、実際このように設計すると、R10の凹形状を削り出すためにはNC旋盤による加工が必要となるので、プログラムを作成しなければならないなど、工数がかかってしまいます。
コストダウン事例
After
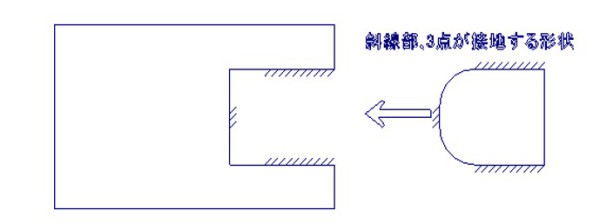
このような場合は、相手物の形状に合わせて設計を行うのではなく、必要とされる機能に合わせて柔軟に形状を変更することがコストアップを回避することに繋がります。
例えば、凹形状をRを持たせるのではなく角形状とします。挿入する部品との接点は面ではなく3点で接することになりますが、こうした形状にするとNC旋盤ではなく汎用旋盤で加工ができるので、プログラム作成に要する時間が削減でき、切削加工時間を大幅に短縮することが可能です。
今回は相手の形状に合わせるのではなく、必要とされる機能に合わせて柔軟に形状を検討する、という事をお伝えしました。実際のところ、面で支える方がもちろん確実に固定できますが、位置決めなど単純な固定であれば3点でも十分なケースは多くあります。機械加工+溶接.comを運営する三栄製作所では、日々お客様からお送り頂く設計図面に対して、お客様の使用環境などもお聞きしながら、VE提案を行っております。お気軽にお問合せください。