Before
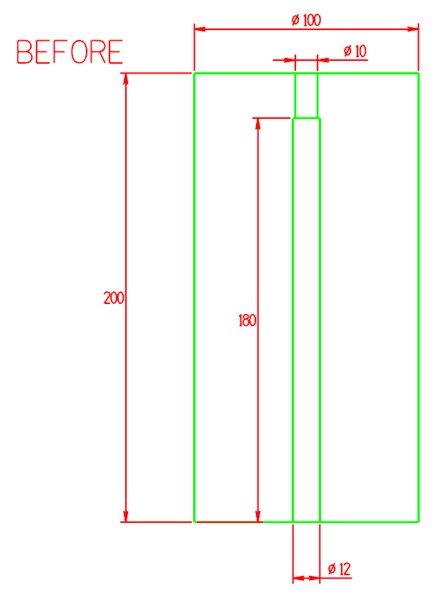
切削加工において深穴の加工が必要な場合、細ければ細いほど、あるいは深ければ深いほど加工難易度が高くなりますが、今回はそんな深穴加工の中でも段差のついた加工のコストダウン事例をお伝えしたいと思います。
まずBeforeの図をご覧ください。こちらはφ100×200の円筒形状のワークに、φ12の深穴とφ10の穴が設計されています。φ100×200に対してφ12の穴を貫通させることも難易度は高くなりますが、このような上下の穴径が違うケースでは、一方向から深さ180mmの穴を加工しなければならない為、ドリルの切削リスクが高まり、その結果加工コストが上昇してしまいます。
コストダウン事例
After
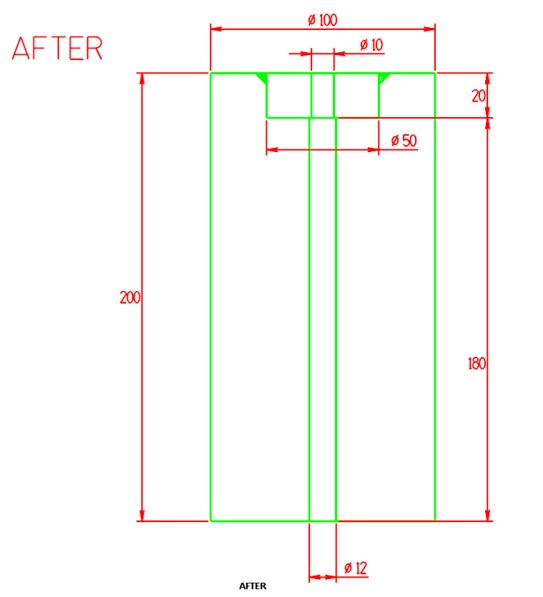
こうした深穴かつ段差がつくようなケースでは、After図のように分割構造とします。このような構造にすると、φ12×180の深穴は比較的容易に加工することが可能となり、φ10の穴加工を施した厚いワッシャー形状のものを溶接して取り付ければ、当初要求されていた形状の加工難易度を下げ、同時にコストも下げることが可能となります。
深穴加工に同軸度などの幾何公差、はめ合い公差などが設定されている場合は分割・溶接構造にすると対応できないケースもありますが、こうした分割・溶接構造にすることでのコストダウン方法を知っているか知らないかで、機械部品のコストは大幅に変わります。機械加工+溶接.comを運営する三栄製作所では、こうしたコストダウン提案を日々行っておりますので、マシニング加工・旋盤加工のコストダウンのご相談がございましたらお気軽にご連絡ください。