Before
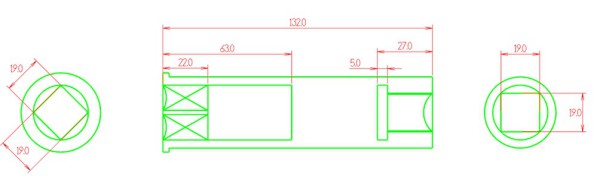
今回は、スロッターによる四角穴加工を設計する際のコストダウン事例についてお伝え致します。まずはBeforeの図をご覧ください。
この図面のように□19の四角穴を設計した場合、加工方法としは、
①まずφ19で下穴加工を行う
②その後、スロッター加工を行う
という加工手順になりますが、スロッター加工を行う立場からすると、ぴったり□19に仕上げなければならないため、切削抵抗・加工負荷がどうしてもかかってしまい、その結果、刃持ちが悪くなります。
コストダウン事例
After
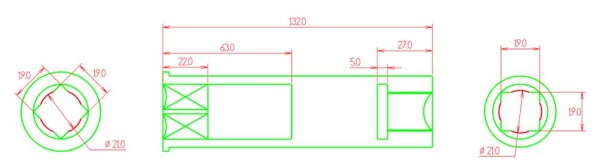
スロッタ―加工が必要なケースは、この四角穴に対象物を挿入してトルクをかけることが想定されますが、そこまでの強度ががない場合は、仕上げ幅に対して下穴径を可能な範囲で大きくする、つまりAfter図のような形状に変更するとスロッター加工の刃持ちと精度が安定し、コストダウンになります。
この場合の加工手順は、
①□19 の場合は、下穴φ21で加工を行う。
②その後、□19にてスロッター加工を行う。
こうすることで、スロッター加工における切削抵抗・加工負荷が下がるので刃持ちが良くなり、コストダウンになります。さらに、下穴加工についてもφ19からφ21に変更を行うので、旋盤加工においても加工難易度・加工時間が下がります。
スロッタ―加工はトルクがかかる箇所に採用されるため、今回ご紹介した案はすべてに適用できる訳ではありませんが、強度など使用上で許容出来る場合は、当たり面積が小さくなるがコストダウンに繋がります。