Before
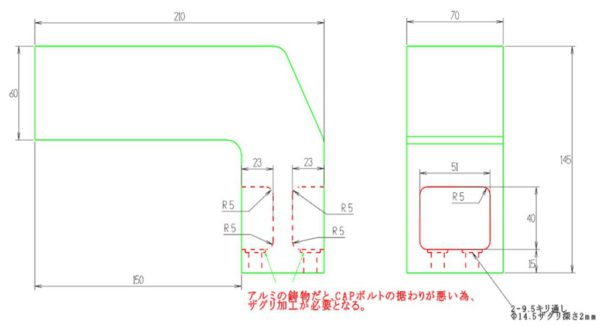
今回は、鋳物やダイカストで作っていた製品を、古くて型が無いなどの理由で全切削加工を行う必要がある場合のコストダウン提案事例をお伝えいたします。
Beforeの図をご覧ください。この製品は鋳物になりますが、他部品の取付用に内側に追加工でザグリを入れるよう設計されています。
これは、鋳物やダイカストを吹いたままの状態では面荒度が悪くキャップボルトの座りが悪くなるため、追加工を行うことでキャップボルトの座りを向上させ、部品をしっかり取り付けられるように考慮されているからです。
コストダウン事例
After
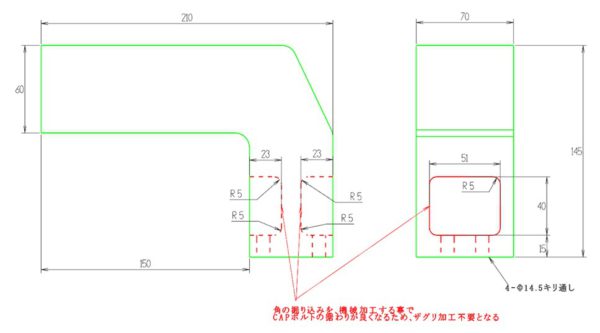
Beforeで説明したように、鋳物やダイカストでは追加工が必要になりますが、全切削で行う場合には、このザグリが不要となりコストダウンできるケースもあります。
Afterの図では、Beforeにあったザグリを無くした設計になっています。
これは、鋳物やダイカストではなく削り出しで機械加工を行った場合は、そもそも面粗度が出るので、ザグリを行わなくともキャップボルトの座りは問題ない場合があります。
今回のケースではお客様に使用状況をお聞きした上でザグリ無しでご提案したところ、設計変更を行って頂きました。これにより加工工程が削減され、コストダウンにつながりました。
鋳物やダイカストは、古い製品の場合は木型や金型が無い・使えない、あるいは数が少ないので対応不可などの理由で全切削で加工を行うこともあります。その際には、図面そのままで製作するのではなく、必要に応じて設計変更を検討することをご提案いたします。
今回のようにそもそもザグリ加工が不要になるケースのほか、全切削では加工できない形状・箇所ということがあるからです。
三栄製作所では、お客様とコミュニケーションを行う中で最適な形状をご提案いたしますので、鋳物・ダイカストの再製作などでお困りの場合は、お気軽にお声がけください。小さいワークなら、型の償却が終わっていても、機械加工が安いかもしれません。
今回のようにそもそもザグリ加工が不要になるケースのほか、全切削では加工できない形状・箇所ということがあるからです。
三栄製作所では、お客様とコミュニケーションを行う中で最適な形状をご提案いたしますので、鋳物・ダイカストの再製作などでお困りの場合は、お気軽にお声がけください。小さいワークなら、型の償却が終わっていても、機械加工が安いかもしれません。